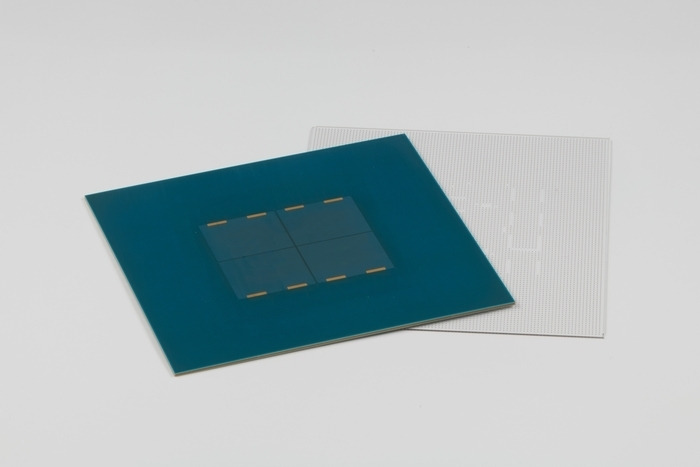
사파이어 웨이퍼와 다이아몬드 웨이퍼
두 웨이퍼 모두 차세대 반도체 소자 및 첨단 산업 분야에서 중요한 기판 소재로 주목받고 있지만, 각기 다른 특성과 응용 분야를 가지고 있습니다. 두 웨이퍼의 특징, 장단점, 그리고 본딩 방법까지 자세히 비교 분석하여 궁금증을 해소해 드리겠습니다.
1. 사파이어 웨이퍼 (Sapphire Wafer)
사파이어는 단결정 산화알루미늄(Al₂O₃)으로, 뛰어난 광학적, 화학적, 기계적 특성을 가진 소재입니다. 특히 청색 LED (Blue LED) 기판 소재로 널리 사용되면서 그 중요성이 더욱 커졌습니다.
- 사파이어의 주요 특징
- 높은 광 투과율 (High Optical Transmission): 자외선부터 적외선 영역까지 넓은 파장 범위에서 빛을 잘 투과합니다. 특히 청색 파장 영역에서의 투과율이 높아 LED 소자에 적합합니다.
- 화학적 안정성 (Chemical Stability): 대부분의 화학 물질에 반응하지 않아 내화학성이 우수합니다. 고온, 부식 환경에서도 안정적인 특성을 유지합니다.
- 높은 경도 및 강도 (High Hardness & Strength): 모스 경도 9로 다이아몬드 다음으로 단단한 물질 중 하나입니다. 긁힘에 강하고 기계적 강도가 높아 안정적인 공정이 가능합니다.
- 우수한 절연 특성 (Excellent Electrical Insulation): 전기 절연성이 뛰어나 반도체 소자의 절연 기판으로 활용될 수 있습니다.
- 적당한 열 전도율 (Moderate Thermal Conductivity): 실리콘보다는 열전도율이 높지만, 다이아몬드보다는 낮습니다. LED 소자의 열 방출에 어느 정도 기여합니다.
- 사파이어 웨이퍼의 장점
- LED 산업의 핵심 소재: 특히 청색 LED, 백색 LED 제조에 필수적인 기판 소재입니다. 저렴한 가격으로 대량 생산이 가능하며, LED 소자의 광효율 향상에 기여합니다.
- 광학 소자 응용에 유리: 높은 광 투과율과 화학적 안정성 덕분에 광학 창, 렌즈, 프리즘 등 다양한 광학 소자 제작에 적합합니다.
- RF 소자 기판으로 활용: 우수한 절연 특성과 고주파 특성을 활용하여 RF (Radio Frequency) 소자, 전력 반도체 소자 기판으로도 응용됩니다.
- 넓은 면적 웨이퍼 생산 가능: 다이아몬드 웨이퍼에 비해 비교적 넓은 면적의 웨이퍼 (최대 12인치) 생산이 가능하여 대량 생산에 유리합니다.
- 결정 성장 기술 발달: 결정 성장 기술 (키스토폴로스법, 열교환법 등) 이 발달하여 대구경, 고품질의 사파이어 단결정 웨이퍼 생산이 용이합니다.
- 사파이어 웨이퍼의 단점
- 낮은 열전도율: 다이아몬드, 실리콘 카바이드 등에 비해 열전도율이 낮아 고전력, 고집적 소자의 방열에는 한계가 있습니다.
- 실리콘과의 격자 불일치 및 열팽창 계수 차이: 실리콘 기반 소자 제작 시 격자 불일치 및 열팽창 계수 차이로 인해 결함 발생 및 잔류 응력 문제가 발생할 수 있습니다.
- 높은 경도로 인한 가공의 어려움: 매우 단단하여 웨이퍼 가공 (연마, 식각 등) 이 어렵고 비용이 많이 들 수 있습니다.
- 소재 가격 상승 가능성: 사파이어 원료 가격 변동 및 수요 증가에 따라 웨이퍼 가격이 상승할 수 있습니다.
- 사파이어 웨이퍼의 주요 응용 분야
- LED (Light Emitting Diode): 청색 LED, 백색 LED, UV LED 등 조명, 디스플레이, 센서, 의료 분야에 널리 사용되는 LED 소자의 기판으로 가장 많이 활용됩니다.
- RF 소자 (Radio Frequency Devices): 고주파 전력 증폭기 (High Power Amplifier, HPA), RF 필터 등 통신, 레이더 시스템에 사용되는 RF 소자의 기판으로 응용됩니다.
- 광학 소자 (Optical Components): 광학 창 (Optical Window), 렌즈 (Lens), 프리즘 (Prism), 광도파로 (Optical Waveguide) 등 다양한 광학 소자 제작에 사용됩니다. 스마트폰 카메라 렌즈 커버, 고출력 레이저 광학계 등 다양한 분야에 적용됩니다.
- 전력 반도체 소자 (Power Semiconductor Devices): 고전압, 고전류 전력 반도체 소자 (MOSFET, IGBT 등) 의 기판으로 연구 개발이 진행되고 있습니다.
- 센서 (Sensors): 고온, 부식 환경에서 작동하는 센서, 압력 센서, 온도 센서 등의 기판으로 활용됩니다.
- 사파이어 웨이퍼 본딩 방법
- 접착제 본딩 (Adhesive Bonding): 에폭시, 아크릴, 실리콘 기반 접착제를 사용하여 비교적 간단하게 본딩하는 방법입니다. 저온 공정이 가능하지만, 접착제의 열적, 기계적 특성이 제한적일 수 있습니다.
- 양극 접합 (Anodic Bonding): 사파이어와 유리, 금속 등을 접합할 때 사용되는 방법입니다. 고온에서 전기장을 가하여 화학적 결합을 유도합니다. 높은 본딩 강도를 얻을 수 있지만, 접합 가능한 재료가 제한적입니다.
- 직접 본딩 (Direct Bonding): 사파이어 웨이퍼 표면을 활성화시킨 후 직접 접합하는 방법입니다. 접착제나 중간층 없이 본딩하여 우수한 열적, 전기적 특성을 얻을 수 있습니다. 표면 활성화 기술 (플라즈마 처리, 이온빔 조사 등) 이 필요하며, 고도의 표면 청정도가 요구됩니다.
- 금속 중간층 본딩 (Metal Interlayer Bonding): 금속 박막 (Au, Cu, Ti 등) 을 중간층으로 사용하여 본딩하는 방법입니다. 금속 중간층은 접착력을 향상시키고 열팽창 계수 차이를 완화하는 역할을 합니다. 확산 접합, 공융 접합, 열압착 접합 등 다양한 방법이 사용될 수 있습니다.
- 사파이어 웨이퍼는 다양한 재료와 본딩될 수 있으며, 주로 다음과 같은 방법들이 사용됩니다.
2. 다이아몬드 웨이퍼 (Diamond Wafer)
다이아몬드는 탄소 동소체 중 하나로, 자연계에서 가장 단단한 물질이며, 뛰어난 물리적, 화학적 특성을 자랑합니다. 차세대 반도체 기판 소재, 첨단 광학 소자, 양자 컴퓨팅 소자 등 다양한 분야에서 혁신적인 응용 가능성을 제시하고 있습니다.
- 다이아몬드의 주요 특징
- 탁월한 열전도율 (Exceptional Thermal Conductivity): 자연계에서 가장 높은 열전도율을 가집니다 (실리콘의 5배 이상). 반도체 소자에서 발생하는 열을 효율적으로 방출하여 성능 향상 및 수명 연장에 크게 기여합니다.
- 높은 전하 이동 속도 및 넓은 밴드갭 (High Carrier Mobility & Wide Bandgap): 실리콘 대비 높은 전하 이동 속도와 넓은 밴드갭을 가져 고주파, 고전압, 고온 동작 소자 제작에 유리합니다. 차세대 전력 반도체, 통신 소자, 센서 등에 적합합니다.
- 극강의 경도 및 강성 (Extreme Hardness & Stiffness): 모스 경도 10으로 자연계 최고 경도를 자랑하며, 기계적 강성 또한 매우 높습니다. 극한 환경에서도 안정적인 소자 구현이 가능합니다.
- 뛰어난 화학적 안정성 (Excellent Chemical Inertness): 화학적으로 매우 안정적이며, 강산, 강알칼리, 고온 환경에서도 부식되지 않습니다. 극한 환경 응용에 적합합니다.
- 넓은 광학 투과 영역 (Wide Optical Transparency Window): 자외선부터 테라헤르츠파 영역까지 넓은 파장 범위에서 빛을 투과합니다. 광학 소자, 센서, 레이저 소자 등 다양한 광학 분야에 응용될 수 있습니다.
- 다이아몬드 웨이퍼의 장점
- 최고의 열 관리 성능: 탁월한 열전도율은 고전력, 고집적 소자의 방열 문제를 획기적으로 해결할 수 있습니다. 소자의 성능 한계를 극복하고, 에너지 효율을 극대화할 수 있습니다.
- 차세대 반도체 소자 가능성: 높은 전하 이동 속도와 넓은 밴드갭은 실리콘의 한계를 뛰어넘는 차세대 반도체 소자 (고주파, 고전압, 고온 소자) 구현을 가능하게 합니다. 6G/7G 통신, 차세대 전력 반도체, 극한 환경 센서 등 미래 기술 발전에 핵심적인 역할을 할 수 있습니다.
- 양자 소자 응용: 다이아몬드 내 질소-공극 (Nitrogen-Vacancy, NV) 센터는 양자 컴퓨팅, 양자 센싱, 양자 통신 등 차세대 양자 기술 소자 구현에 중요한 플랫폼을 제공합니다.
- 극한 환경 소자: 극강의 경도, 강성, 화학적 안정성은 극한 환경 (고온, 고압, 부식 환경, 방사선 환경 등) 에서 작동하는 특수 목적 소자 제작에 이상적인 소재입니다. 우주항공, 심해 탐사, 원자력 발전소 등 극한 환경에서 요구되는 고성능, 고신뢰성 소자 개발에 기여할 수 있습니다.
- 생체 적합성: 다이아몬드는 생체 적합성이 높아 의료용 임플란트, 바이오 센서 등 의료 분야 응용 가능성도 높습니다.
- 다이아몬드 웨이퍼의 단점
- 매우 높은 생산 비용: 천연 다이아몬드는 희귀하고, 인공 다이아몬드 웨이퍼 생산 기술 또한 매우 복잡하고 고가입니다. 웨이퍼 가격이 매우 높아 대량 생산 및 상용화에 어려움이 있습니다.
- 작은 웨이퍼 크기: 현재 기술로는 대면적 다이아몬드 단결정 웨이퍼 생산이 매우 어렵습니다. 주로 작은 크기의 웨이퍼 (2인치, 4인치 이하) 만 생산 가능하여 대량 생산에 불리합니다.
- 낮은 n형 도핑 효율 및 불균일성: 다이아몬드 반도체 소자 제작 시 n형 도핑 효율이 매우 낮고, 도핑 균일성 확보가 어렵습니다. 소자 성능 및 신뢰성 확보에 걸림돌이 됩니다.
- 재료 이종 접합의 어려움: 다이아몬드는 화학적으로 매우 안정적이어서 다른 재료와 직접 본딩하기 어렵습니다. 효과적인 본딩 기술 개발이 필요합니다.
- 높은 결정 결함 밀도: 다이아몬드 단결정 성장 과정에서 결정 결함이 발생하기 쉽고, 결함 밀도 제어가 어렵습니다. 웨이퍼 품질 및 소자 성능에 영향을 미칠 수 있습니다.
- 다이아몬드 웨이퍼의 주요 응용 분야
- 고전력/고주파 반도체 소자 (High Power/High Frequency Devices): 차세대 전력 반도체 (GaN on Diamond HEMT 등), 고주파 통신 소자, 레이더 소자 등 고성능, 고효율 소자 제작에 응용됩니다.
- 고온/극한 환경 소자 (High Temperature/Extreme Environment Devices): 고온, 방사선 환경, 화학적 부식 환경 등 극한 조건에서 작동하는 센서, 트랜지스터, 다이오드 등 특수 목적 소자에 활용됩니다.
- 양자 컴퓨팅/센싱 소자 (Quantum Computing/Sensing Devices): NV 센터 기반 양자 비트, 양자 센서, 양자 현미경 등 차세대 양자 기술 소자 개발에 핵심적인 역할을 합니다.
- 고성능 광학 소자 (High Performance Optical Devices): 고출력 레이저, 고성능 광학 센서, 극자외선 (EUV) 광학 소자 등 첨단 광학 시스템에 응용될 수 있습니다.
- 생체 의료 기기 (Biomedical Devices): 생체 이식형 전극, 약물 전달 시스템, 바이오 센서 등 생체 적합성이 요구되는 의료 기기 분야에 적용 가능합니다.
- 고전력/고주파 반도체 소자 (High Power/High Frequency Devices): 차세대 전력 반도체 (GaN on Diamond HEMT 등), 고주파 통신 소자, 레이더 소자 등 고성능, 고효율 소자 제작에 응용됩니다.
- 다이아몬드 웨이퍼 본딩 방법
- 금속 중간층 본딩 (Metal Interlayer Bonding): Ti, Au, Cu, Sn 등 다양한 금속 박막을 중간층으로 사용하여 다이아몬드 웨이퍼를 다른 재료 (반도체 칩, 다른 웨이퍼 등) 와 본딩하는 방법입니다. 확산 접합, 공융 접합, 열압착 접합 등 다양한 기술이 활용됩니다. 금속 중간층은 접착력 향상 및 열팽창 계수 완화 역할을 합니다.
- 활성 금속 브레이징 (Active Metal Brazing): 활성 금속 (Ti, Zr 등) 이 포함된 브레이징 재료를 사용하여 다이아몬드와 금속, 세라믹 등을 접합하는 방법입니다. 활성 금속은 다이아몬드 표면과의 반응성을 높여 접착력을 향상시킵니다. 고온 공정이 필요하며, 높은 본딩 강도를 얻을 수 있습니다.
- 표면 활성화 본딩 (Surface Activated Bonding, SAB): 플라즈마, 이온빔 등을 이용하여 다이아몬드 표면을 활성화시킨 후 상온 또는 저온에서 본딩하는 방법입니다. 표면 활성화는 다이아몬드 표면의 반응성을 높이고, 접착력을 향상시키는 효과가 있습니다. 금속 중간층 없이 직접 본딩이 가능하며, 저온 공정이 가능하다는 장점이 있습니다.
- 하이브리드 본딩 (Hybrid Bonding): 두 가지 이상의 본딩 기술을 결합하여 장점을 극대화하는 방법입니다. 예를 들어, 표면 활성화 기술과 금속 중간층 본딩을 결합하여 저온, 고신뢰성 다이아몬드 본딩을 구현할 수 있습니다.
- 다이아몬드 웨이퍼는 화학적 불활성 때문에 직접 본딩이 어렵고, 주로 중간층을 사용하는 본딩 방법이 연구되고 있습니다.
3. 사파이어 웨이퍼 vs 다이아몬드 웨이퍼 비교표
열전도율 | 보통 (실리콘보다 높음) | 탁월 (자연계 최고) |
전하 이동 속도 | 보통 (실리콘보다 낮음) | 높음 (실리콘보다 높음) |
밴드갭 | 넓음 (실리콘보다 넓음) | 매우 넓음 (실리콘보다 훨씬 넓음) |
경도 | 매우 높음 (모스 경도 9) | 최고 (모스 경도 10) |
화학적 안정성 | 우수 | 탁월 |
광 투과율 | 넓은 영역에서 우수 (특히 청색 파장) | 매우 넓은 영역에서 우수 (UV ~ THz) |
웨이퍼 크기 | 최대 12인치 | 주로 2-4인치 이하 |
생산 비용 | 비교적 저렴 | 매우 고가 |
결정 결함 | 비교적 적음 | 비교적 많음 |
도핑 | 비교적 용이 | n형 도핑 어려움, 불균일성 |
본딩 | 비교적 용이 (접착제, 양극 접합 등) | 어려움 (금속 중간층, 표면 활성화 필요) |
주요 응용 분야 | LED, 광학 소자, RF 소자 | 고전력/고주파 소자, 양자 소자, 극한 환경 소자 |
상용화 수준 | 높음 (LED 시장 주도) | 초기 단계 (고성능 특수 분야 중심) |
4. 비용 비교
일반적으로 사파이어 웨이퍼는 다이아몬드 웨이퍼에 비해 훨씬 저렴합니다. 사파이어는 결정 성장 기술이 발달하여 대량 생산이 가능하고, 원료 가격도 상대적으로 낮습니다. 반면, 다이아몬드 웨이퍼는 생산 기술이 복잡하고, 고품질 웨이퍼 생산 수율이 낮아 가격이 매우 높게 형성됩니다.
5. 결론
사파이어 웨이퍼와 다이아몬드 웨이퍼는 각각 고유한 장단점을 가지고 있으며, 응용 분야에 따라 최적의 선택이 달라집니다.
- 사파이어 웨이퍼: 가격 경쟁력과 LED 소자에 최적화된 특성을 바탕으로 LED 조명 시장을 비롯한 광학 소자, RF 소자 분야에서 널리 사용됩니다. 비교적 저렴한 비용으로 넓은 면적의 웨이퍼를 얻을 수 있어 대량 생산에 유리하며, 다양한 본딩 방법이 개발되어 활용되고 있습니다.
- 다이아몬드 웨이퍼: 탁월한 열 관리 성능과 차세대 반도체 소자 가능성을 바탕으로 고성능, 고신뢰성이 요구되는 첨단 분야에서 잠재력이 매우 큽니다. 특히 고전력/고주파 소자, 양자 소자, 극한 환경 소자 분야에서 혁신적인 발전을 가져올 것으로 기대됩니다. 하지만 높은 생산 비용과 작은 웨이퍼 크기, 본딩 기술의 어려움 등 극복해야 할 과제가 남아있습니다.
어떤 웨이퍼를 선택할지는 소자의 성능 요구 조건, 가격 제약, 생산량, 응용 분야 등을 종합적으로 고려하여 결정해야 합니다. 만약 높은 열 방출 특성이 필수적이고, 최고의 성능을 추구하는 분야라면 다이아몬드 웨이퍼가 매력적인 선택이 될 수 있습니다. 반면, 가격 경쟁력이 중요하고, 대량 생산이 필요한 LED 조명 분야 등에서는 사파이어 웨이퍼가 여전히 핵심적인 역할을 할 것입니다.
더 궁금한 점이나 특정 응용 분야에 대한 질문이 있으시면 언제든지 다시 문의해주세요.
실리콘 웨이퍼 (Silicon Wafer, Si Wafer) 와 실리콘 카바이드 웨이퍼 (Silicon Carbide Wafer, SiC Wafer)
두 웨이퍼 모두 반도체 산업에서 매우 중요한 기판 소재이지만, 각기 다른 특성과 활용 분야를 가지고 있습니다. 특히 최근에는 SiC 웨이퍼가 차세대 전력 반도체 소재로 각광받으면서 그 중요성이 더욱 커지고 있습니다. 실리콘 웨이퍼와 SiC 웨이퍼의 특징, 장단점, 응용 분야, 그리고 본딩 방법에 대해 자세히 비교 분석하여 사용자의 궁금증을 해소해 드리겠습니다.
1. 실리콘 웨이퍼 (Silicon Wafer, Si Wafer)
실리콘 (Si) 은 반도체 산업의 가장 핵심적인 소재입니다. 지구상에서 두 번째로 풍부한 원소이며, 반도체 특성을 가지면서도 비교적 저렴하고 가공이 용이하여 오랫동안 반도체 산업을 지배해 왔습니다. 실리콘 웨이퍼는 이러한 실리콘 단결정을 얇게 절단하여 만든 기판으로, 대부분의 반도체 칩 제조에 사용됩니다.
- 실리콘의 주요 특징
- 적절한 밴드갭 (Appropriate Bandgap): 1.1 eV 의 밴드갭은 반도체 소자 동작에 적합한 수준입니다. 너무 넓지도 좁지도 않아 다양한 소자 설계에 유연성을 제공합니다.
- 적당한 전하 이동 속도 (Moderate Carrier Mobility): 전하 이동 속도는 중간 정도이지만, 충분히 빠른 속도를 제공하여 대부분의 전자 소자 요구 사항을 충족합니다.
- 풍부한 매장량 및 저렴한 가격 (Abundant & Low Cost): 지구상에 풍부하게 존재하여 원료 수급이 용이하고, 웨이퍼 생산 비용이 상대적으로 저렴합니다. 반도체 대량 생산에 유리한 가장 큰 장점입니다.
- 우수한 가공성 (Excellent Processability): 결정 성장, 웨이퍼 가공 (연마, 식각, 박막 증착 등), 도핑 등 반도체 제조 공정에 최적화된 기술들이 잘 발달되어 있습니다. 미세 공정 기술 구현에 용이합니다.
- 자연 산화막 (Native Oxide - SiO₂): 실리콘은 자연적으로 안정적인 절연막인 이산화규소 (SiO₂) 를 형성합니다. SiO₂는 게이트 절연막, 소자 보호막 등 다양한 용도로 활용되어 실리콘 소자 제작에 매우 유리합니다.
- 실리콘 웨이퍼의 장점
- 압도적인 시장 점유율 및 성숙한 기술: 반도체 산업의 역사를 이끌어온 소재로, 웨이퍼 생산부터 소자 제작, 패키징까지 전반적인 기술 생태계가 완벽하게 구축되어 있습니다. 기술적인 노하우와 인프라가 풍부하여 안정적인 대량 생산이 가능합니다.
- 저렴한 가격으로 대량 생산 가능: 다른 화합물 반도체 소재에 비해 웨이퍼 가격이 훨씬 저렴하여 대량 생산이 필요한 범용 반도체 칩 (메모리, CPU, 센서, 로직 칩 등) 제조에 가장 경제적입니다.
- 고집적 회로 (VLSI) 제작에 최적화: 미세 공정 기술, 도핑 기술, 절연막 형성 기술 등 고집적 회로 제작에 필요한 핵심 기술들이 실리콘 기반으로 발전되어 왔습니다. 첨단 미세 공정 기술을 가장 잘 활용할 수 있는 소재입니다.
- 다양한 응용 분야: 디지털 회로, 아날로그 회로, 메모리 소자, 센서, 광소자 등 거의 모든 종류의 반도체 소자에 적용될 수 있는 범용적인 소재입니다.
- 실리콘 웨이퍼의 단점
- 낮은 밴드갭 및 낮은 항복 전압: SiC, GaN 등 와이드 밴드갭 (Wide Bandgap, WBG) 반도체에 비해 밴드갭이 좁고 항복 전압이 낮아 고전압, 고전력 소자에는 한계가 있습니다. 전력 손실이 크고, 고온 동작 특성이 떨어집니다.
- 낮은 열전도율: SiC, 다이아몬드 등에 비해 열전도율이 낮아 고전력 소자에서 발생하는 열을 효과적으로 방출하기 어렵습니다. 소자의 성능 저하 및 수명 단축을 유발할 수 있습니다.
- 높은 온도에서 성능 저하: 고온 (150℃ 이상) 에서 캐리어 이동 속도 감소, 누설 전류 증가 등 소자 특성이 저하됩니다. 고온 환경에서 안정적인 동작이 어렵습니다.
- 광전자 소자 효율 제한: 간접 밴드갭 (Indirect Bandgap) 구조를 가지고 있어 빛을 효율적으로 흡수하거나 방출하기 어렵습니다. LED, 레이저 다이오드 등 광전자 소자 효율 향상에 제약이 있습니다.
- 실리콘 웨이퍼의 주요 응용 분야
- 집적 회로 (Integrated Circuits, ICs): CPU, GPU, 메모리 (DRAM, NAND Flash), 마이크로컨트롤러 (MCU), 시스템온칩 (SoC), ASIC 등 거의 모든 종류의 집적 회로 칩의 기판으로 사용됩니다.
- 개별 소자 (Discrete Devices): 트랜지스터, 다이오드, 사이리스터 등 개별 반도체 소자 제작에도 널리 사용됩니다.
- 센서 (Sensors): 이미지 센서 (CMOS 이미지 센서, CCD 이미지 센서), MEMS 센서 (가속도 센서, 자이로 센서, 압력 센서), 환경 센서 등 다양한 센서 소자의 기판으로 활용됩니다.
- 태양 전지 (Solar Cells): 결정질 실리콘 태양 전지 (단결정, 다결정) 는 태양광 발전 시장에서 가장 큰 비중을 차지하고 있습니다.
- 광통신 소자 (Optical Communication Devices): 광검출기 (Photodetector), 광스위치 (Optical Switch) 등 광통신 시스템에 사용되는 일부 소자에 실리콘 웨이퍼가 활용됩니다. (주로 수동 소자 또는 실리콘 포토닉스 기술)
- 집적 회로 (Integrated Circuits, ICs): CPU, GPU, 메모리 (DRAM, NAND Flash), 마이크로컨트롤러 (MCU), 시스템온칩 (SoC), ASIC 등 거의 모든 종류의 집적 회로 칩의 기판으로 사용됩니다.
- 실리콘 웨이퍼 본딩 방법
- 실리콘 직접 본딩 (Silicon Direct Bonding, SDB): 두 실리콘 웨이퍼 표면을 활성화시킨 후 직접 접합하는 방법입니다. 접착제나 중간층 없이 본딩하여 우수한 계면 특성, 높은 본딩 강도, 뛰어난 열적, 전기적 특성을 얻을 수 있습니다. 3D 집적 회로 (3D IC), MEMS, SOI (Silicon-On-Insulator) 웨이퍼 제작 등에 널리 사용됩니다.
- 양극 접합 (Anodic Bonding): 실리콘 웨이퍼와 유리, 금속 등을 접합할 때 사용되는 방법입니다. 고온에서 전기장을 가하여 화학적 결합을 유도합니다. MEMS, 센서, 마이크로 유체 소자 제작 등에 활용됩니다.
- 접착제 본딩 (Adhesive Bonding): 에폭시, 아크릴, 폴리이미드 등 유기 접착제를 사용하여 비교적 간단하게 본딩하는 방법입니다. 저온 공정이 가능하지만, 접착제의 열적, 기계적 특성이 제한적일 수 있습니다. 이종 재료 접합, 웨이퍼 레벨 패키징 등에 응용됩니다.
- 금속 중간층 본딩 (Metal Interlayer Bonding): 금속 박막 (Au, Cu, Al, Sn 등) 을 중간층으로 사용하여 본딩하는 방법입니다. 금속 중간층은 접착력 향상, 전기적 연결, 열팽창 계수 완화 등의 역할을 합니다. 확산 접합, 공융 접합, 열압착 접합 등 다양한 기술이 사용됩니다. 이종 재료 접합, 고전력 소자 패키징 등에 활용됩니다.
- 하이브리드 본딩 (Hybrid Bonding): 유전체 직접 본딩과 금속 본딩을 결합하여 고밀도 수직 상호 연결을 구현하는 첨단 본딩 기술입니다. 차세대 3D 집적 회로 (3D IC) 제작에 핵심적인 역할을 합니다. 실리콘 웨이퍼 뿐 아니라, 이종 웨이퍼 (heterogeneous wafer) 본딩에도 적용 가능성이 높습니다.
- 실리콘 직접 본딩 (Silicon Direct Bonding, SDB): 두 실리콘 웨이퍼 표면을 활성화시킨 후 직접 접합하는 방법입니다. 접착제나 중간층 없이 본딩하여 우수한 계면 특성, 높은 본딩 강도, 뛰어난 열적, 전기적 특성을 얻을 수 있습니다. 3D 집적 회로 (3D IC), MEMS, SOI (Silicon-On-Insulator) 웨이퍼 제작 등에 널리 사용됩니다.
- 실리콘 웨이퍼는 다양한 재료와 본딩될 수 있으며, 반도체 공정 기술 발달과 함께 다양한 본딩 방법이 개발되어 활용되고 있습니다.
2. 실리콘 카바이드 웨이퍼 (Silicon Carbide Wafer, SiC Wafer)
실리콘 카바이드 (SiC) 는 실리콘 (Si) 과 탄소 (C) 화합물로, 와이드 밴드갭 (Wide Bandgap, WBG) 반도체 소재의 대표 주자입니다. 실리콘의 단점을 극복하고 고전력, 고주파, 고온 환경에서 뛰어난 성능을 발휘하여 차세대 전력 반도체, 고주파 통신 소자, 극한 환경 센서 등 다양한 분야에서 주목받고 있습니다.
- 실리콘 카바이드의 주요 특징
- 넓은 밴드갭 (Wide Bandgap): 실리콘 (1.1 eV) 보다 약 3배 넓은 밴드갭 (3.26 eV, 4H-SiC 기준) 을 가집니다. 고온, 고전압 환경에서 누설 전류가 적고, 고주파 동작 특성이 우수합니다. 전력 반도체 소자 효율 향상에 핵심적인 장점입니다.
- 높은 항복 전압 (High Breakdown Voltage): 실리콘 대비 약 10배 높은 항복 전압을 가집니다. 고전압 전력 소자 제작에 유리하며, 전력 변환 효율 및 안정성을 높여줍니다.
- 높은 열전도율 (High Thermal Conductivity): 실리콘보다 약 3배 높은 열전도율을 가집니다. 고전력 소자에서 발생하는 열을 효과적으로 방출하여 소자 성능 저하 및 수명 단축을 방지합니다.
- 높은 전자 포화 속도 (High Electron Saturation Velocity): 고주파 동작 특성이 우수하여 5G/6G 통신 등 차세대 통신 소자, 고주파 전력 증폭기 등에 적합합니다.
- 화학적 안정성 및 고온 안정성 (Chemical & High Temperature Stability): 화학적으로 매우 안정적이며, 고온 (최대 600℃ 이상) 에서도 안정적인 특성을 유지합니다. 극한 환경 소자, 고온 센서 등에 응용 가능합니다.
- 실리콘 카바이드 웨이퍼의 장점
- 차세대 전력 반도체 핵심 소재: SiC MOSFET, SiC SBD (쇼트키 배리어 다이오드) 등 SiC 전력 소자는 기존 실리콘 전력 소자 대비 월등한 성능 (고효율, 고속 스위칭, 저전력 손실) 을 제공합니다. 전기차, 충전 인프라, 신재생 에너지, 산업용 전력 변환 시스템 등 전력 효율이 중요한 분야에서 SiC 채택이 급증하고 있습니다.
- 고주파 소자 응용: 높은 전자 포화 속도와 내열성은 5G/6G 통신, 국방/항공 우주용 레이더 등 고주파 소자 분야에 적합합니다. GaN (질화갈륨) 과 함께 차세대 고주파 소자 시장을 주도할 것으로 예상됩니다.
- 고온, 극한 환경 소자 가능성: 고온 안정성, 화학적 안정성, 방사선 내성 등을 활용하여 고온 센서, 극한 환경용 반도체 소자 개발에 유리합니다.
- 시스템 효율 및 소형화: SiC 소자는 높은 효율과 낮은 전력 손실로 인해 전력 변환 시스템의 효율을 높이고, 냉각 시스템을 간소화하여 시스템 소형화, 경량화에 기여할 수 있습니다.
- 장기적인 비용 절감: 초기 웨이퍼 가격은 비싸지만, 시스템 효율 향상, 에너지 절감, 유지보수 비용 절감 등 장기적인 관점에서 총 소유 비용 (Total Cost of Ownership, TCO) 을 절감할 수 있습니다.
- 차세대 전력 반도체 핵심 소재: SiC MOSFET, SiC SBD (쇼트키 배리어 다이오드) 등 SiC 전력 소자는 기존 실리콘 전력 소자 대비 월등한 성능 (고효율, 고속 스위칭, 저전력 손실) 을 제공합니다. 전기차, 충전 인프라, 신재생 에너지, 산업용 전력 변환 시스템 등 전력 효율이 중요한 분야에서 SiC 채택이 급증하고 있습니다.
- 실리콘 카바이드 웨이퍼의 단점
- 높은 웨이퍼 가격: 실리콘 웨이퍼에 비해 웨이퍼 가격이 매우 비쌉니다. 고온, 장시간 결정 성장 공정, 어려운 웨이퍼 가공 기술 등으로 인해 생산 비용이 높습니다. SiC 웨이퍼 가격은 Si 웨이퍼 대비 수십 배에서 수백 배까지 높을 수 있습니다.
- 작은 웨이퍼 크기: 대구경 SiC 단결정 성장 기술이 아직 초기 단계에 머물러 있어, 주로 작은 크기의 웨이퍼 (6인치, 8인치) 만 상용화되어 있습니다. 대면적 웨이퍼 생산 기술 개발이 시급합니다.
- 결정 결함 및 낮은 수율: SiC 단결정 성장 시 결함 (미세 파이프, 적층 결함 등) 이 발생하기 쉽고, 웨이퍼 수율이 낮습니다. 결정 품질 향상 및 수율 향상이 중요한 과제입니다.
- 가공의 어려움: 매우 단단하고 화학적으로 안정적이어서 웨이퍼 가공 (연마, 식각 등) 이 어렵고, 특수 장비 및 기술이 필요합니다. 웨이퍼 가공 비용 상승의 원인이 됩니다.
- 소자 제작 공정 난이도: SiC 소자 제작 공정 (도핑, 게이트 절연막 형성, 전극 형성 등) 은 실리콘 공정에 비해 난이도가 높고, 최적화된 공정 기술 개발이 필요합니다.
- 실리콘 카바이드 웨이퍼의 주요 응용 분야
- 전력 반도체 (Power Semiconductors): 전기 자동차 (EV) 인버터, 충전기, 전력 변환 장치 (인버터, 컨버터), 산업용 모터 드라이브, 전력 송배전 시스템, 전원 공급 장치 (PSU) 등 고효율 전력 변환 및 제어가 필요한 분야에 SiC 전력 소자가 널리 사용되고 있습니다.
- 고주파 RF 소자 (High Frequency RF Devices): 5G/6G 통신 기지국, 위성 통신, 레이더 시스템, 무선 전력 전송 등 고주파 대역에서 작동하는 통신 및 전력 증폭 소자에 응용됩니다.
- 고온 센서 및 극한 환경 소자 (High Temperature Sensors & Extreme Environment Devices): 자동차 엔진 제어 센서, 항공기 엔진 센서, 산업 플랜트 센서, 우주 탐사 장비, 원자력 발전소 센서 등 고온, 방사선, 화학적 부식 환경에서 작동하는 특수 센서 및 소자에 활용됩니다.
- LED 조명 (LED Lighting): SiC 웨이퍼는 GaN LED 에피택시 기판으로 사용되어 고효율 LED 제작에 기여합니다. 특히 고출력 LED 조명, 자동차 전조등, 특수 조명 분야에서 SiC 기판 LED 가 활용됩니다.
- 전력 반도체 (Power Semiconductors): 전기 자동차 (EV) 인버터, 충전기, 전력 변환 장치 (인버터, 컨버터), 산업용 모터 드라이브, 전력 송배전 시스템, 전원 공급 장치 (PSU) 등 고효율 전력 변환 및 제어가 필요한 분야에 SiC 전력 소자가 널리 사용되고 있습니다.
- 실리콘 카바이드 웨이퍼 본딩 방법
- 직접 본딩 (Direct Bonding): SiC 웨이퍼 표면을 활성화시킨 후 직접 접합하는 방법입니다. SiC-SiC 직접 본딩, SiC-SiO₂ 직접 본딩 등이 연구되고 있으며, 접착제나 중간층 없이 우수한 계면 특성을 얻을 수 있습니다. 표면 활성화 기술 (플라즈마 처리, 화학적 처리 등) 이 중요합니다.
- 금속 중간층 본딩 (Metal Interlayer Bonding): 금속 박막 (Ni, Au, Al, Cu, Ti, Sn 등) 을 중간층으로 사용하여 SiC 웨이퍼를 다른 재료와 접합하는 방법입니다. 확산 접합, 공융 접합, 열압착 접합 등 다양한 기술이 적용됩니다. 금속 중간층은 접착력 향상, 열팽창 계수 완화, 전기적 연결 등의 역할을 합니다.
- 접착제 본딩 (Adhesive Bonding): 에폭시, 폴리이미드 등 유기 접착제를 사용하여 SiC 웨이퍼를 접합하는 방법입니다. 간단하고 저온 공정이 가능하지만, 접착제의 내열성, 열전도율, 신뢰성 등을 고려해야 합니다.
- 하이브리드 본딩 (Hybrid Bonding): 유전체 직접 본딩과 금속 본딩을 결합하여 SiC 웨이퍼의 고밀도 집적을 구현하는 기술입니다. SiC 전력 소자 모듈, 3D SiC 집적 회로 등 차세대 SiC 소자 제작에 적용될 가능성이 높습니다.
- SiC 웨이퍼는 실리콘 웨이퍼와 마찬가지로 다양한 재료와 본딩될 수 있으며, 특히 이종 재료 (Heterogeneous) 집적을 위한 본딩 기술 연구가 활발히 진행되고 있습니다.
3. 실리콘 웨이퍼 vs 실리콘 카바이드 웨이퍼 비교표
밴드갭 | 1.1 eV (좁음) | 3.26 eV (넓음, 4H-SiC 기준) |
항복 전압 | 낮음 | 높음 (실리콘의 약 10배) |
열전도율 | 낮음 | 높음 (실리콘의 약 3배) |
전하 이동 속도 | 보통 | 높음 |
최고 동작 온도 | ~150℃ | ~600℃ 이상 |
웨이퍼 가격 | 저렴 | 고가 (실리콘 대비 수십~수백 배) |
웨이퍼 크기 | 최대 12인치 | 주로 6-8인치 |
결정 결함 | 적음 | 비교적 많음 |
가공성 | 우수 | 어려움 |
도핑 | 용이 | 비교적 어려움 (특히 n형) |
본딩 | 다양한 방법 활용 가능, 직접 본딩 용이 | 직접 본딩, 금속 중간층 본딩 등 연구 활발 |
주요 응용 분야 | IC, 센서, 태양 전지, 범용 반도체 | 전력 반도체, 고주파 소자, 극한 환경 소자 |
시장 점유율 | 압도적 (반도체 시장 대부분) | 빠르게 성장 중 (전력 반도체 시장 중심) |
4. 비용 비교
실리콘 웨이퍼는 실리콘 카바이드 웨이퍼에 비해 압도적으로 저렴합니다. 실리콘은 풍부한 매장량과 성숙된 생산 기술 덕분에 대량 생산이 가능하며, 웨이퍼 가격 경쟁력이 매우 높습니다. 반면, SiC 웨이퍼는 고온, 장시간 결정 성장 공정, 낮은 수율, 어려운 가공 기술 등으로 인해 생산 비용이 높아 웨이퍼 가격이 매우 높습니다. SiC 웨이퍼 가격은 크기, 품질, 폴리타입 (4H, 6H 등) 에 따라 다르지만, 실리콘 웨이퍼 대비 수십 배에서 수백 배까지 높게 형성됩니다.
5. 결론
실리콘 웨이퍼와 실리콘 카바이드 웨이퍼는 각각 뚜렷한 장단점을 가지고 있으며, 응용 분야가 다릅니다.
- 실리콘 웨이퍼 (Si Wafer): 저렴한 가격, 우수한 가공성, 성숙한 기술을 바탕으로 범용 반도체 시장을 지배하고 있습니다. CPU, 메모리, 센서, 로직 칩 등 대부분의 집적 회로 칩은 실리콘 웨이퍼 기반으로 제작되며, 앞으로도 핵심적인 소재 지위를 유지할 것입니다.
- 실리콘 카바이드 웨이퍼 (SiC Wafer): 높은 밴드갭, 높은 항복 전압, 높은 열전도율 등 뛰어난 고전력, 고주파, 고온 특성을 바탕으로 차세대 전력 반도체 시장을 빠르게 확대하고 있습니다. 전기 자동차, 충전 인프라, 신재생 에너지, 5G/6G 통신 등 에너지 효율과 고성능이 중요한 분야에서 SiC 소자의 채택이 증가하면서 SiC 웨이퍼의 중요성은 더욱 커질 것입니다.
사파이어, 다이아몬드 웨이퍼와의 관계:
- 사파이어 웨이퍼: LED 조명 시장에서 핵심적인 역할을 하며, 광학 소자, RF 소자 등 특정 분야에서 강점을 가집니다. 반도체 기판 소재로서 Si, SiC 와는 다른 틈새 시장을 공략하고 있습니다.
- 다이아몬드 웨이퍼: 최고 수준의 열 관리 성능과 극한 환경 특성을 바탕으로 차세대 반도체 소자, 양자 소자 등 매우 고성능, 특수 목적 분야에서 혁신적인 잠재력을 가지고 있습니다. 하지만 높은 가격과 기술적인 난제로 인해 아직 상용화 초기 단계에 머물러 있습니다. Si, SiC, 사파이어 웨이퍼와는 차별화된 최첨단 분야를 목표로 하고 있습니다.
어떤 웨이퍼를 선택할지는 소자의 성능 요구 조건, 가격 목표, 생산량, 응용 분야 등을 종합적으로 고려하여 결정해야 합니다. SiC 웨이퍼는 높은 초기 비용에도 불구하고 시스템 효율 향상, 소형화, 장기적인 비용 절감 효과를 가져올 수 있어, 전력 반도체 시장을 중심으로 빠르게 성장할 것으로 전망됩니다.
더 궁금한 점이나 특정 응용 분야에 대한 질문이 있으시면 언제든지 다시 문의해주세요.
유리 웨이퍼와 유리기판
흔히 혼용되어 사용되기도 하는 용어이지만, 미묘한 차이점과 함께 각각의 특징과 활용 분야가 존재합니다. 유리 웨이퍼와 유리기판의 개념, 제조 과정, 응용 분야, 그리고 차이점을 명확하게 설명하여 궁금증을 해소해 드리겠습니다.
1. 유리기판 (Glass Substrate)
유리기판은 평판 디스플레이 (FPD), 태양 전지, 터치스크린 패널, 센서, 반도체 패키징 등 다양한 산업 분야에서 널리 사용되는 기본적인 유리 소재를 지칭하는 광범위한 용어입니다. 여기서 '기판(substrate)'은 특정 기능성 박막이나 소자를 형성하기 위한 지지체 역할을 하는 판 형태의 재료를 의미합니다. 유리기판은 다양한 종류의 유리 조성과 형태, 크기로 제작될 수 있으며, 특정 응용 분야의 요구 조건에 맞춰 맞춤형으로 설계될 수 있습니다.
- 유리기판의 일반적인 특징:
- 다양한 유리 조성: 소다라임 유리, 붕규산 유리, 무알칼리 유리, 석영 유리, 특수 기능성 유리 등 다양한 유리 조성을 선택하여 응용 분야에 최적화된 기판 제작이 가능합니다. 각 유리 조성마다 고유한 광학적, 열적, 화학적, 기계적 특성을 가집니다.
- 우수한 광학적 특성 (Optical Transparency): 대부분의 유리는 가시광선 영역에서 높은 투과율을 가지며, 특정 유리 (석영 유리, 붕규산 유리 등) 는 자외선, 적외선 영역에서도 투과율이 우수합니다. 디스플레이, 광학 소자, 태양 전지 기판으로 활용되는 중요한 특징입니다.
- 평탄하고 매끄러운 표면 (Flat and Smooth Surface): 정밀 연마 공정을 통해 매우 평탄하고 매끄러운 표면을 얻을 수 있습니다. 박막 증착, 미세 패턴 형성 등 정밀 공정이 필요한 분야에 적합합니다.
- 화학적 안정성 (Chemical Stability): 대부분의 유리는 화학적으로 안정적이며, 다양한 화학 물질에 대한 내성이 우수합니다. 반도체 공정, 디스플레이 공정 등 화학 약품을 사용하는 환경에서 안정적으로 사용될 수 있습니다.
- 절연 특성 (Electrical Insulation): 유리는 전기 절연체이므로, 절연 기판이 필요한 응용 분야에 적합합니다.
- 유리기판의 종류 (유리 조성에 따른 분류):
- 소다라임 유리 (Soda-Lime Glass): 가장 일반적인 유리 조성으로, 저렴한 가격과 비교적 용이한 생산 공정으로 인해 널리 사용됩니다. 일반 창문, 병, 유리 용기 등에 주로 사용되며, 평판 디스플레이 기판, 커버 유리 등 응용 분야도 넓습니다. 하지만 열팽창 계수가 높고, 내열성, 내화학성이 다른 유리에 비해 떨어지는 단점이 있습니다.
- 붕규산 유리 (Borosilicate Glass): 소다라임 유리에 붕산(B₂O₃)을 첨가하여 열팽창 계수를 낮추고 내열성을 향상시킨 유리입니다. 급격한 온도 변화에 강하고, 화학적 안정성도 우수하여 실험 기구, 내열 유리 용기, 고급 조명 기구, LCD 기판 등에 사용됩니다. 대표적인 예시로 파이렉스(Pyrex), 쇼트(Schott)의 보로플로트(Borofloat) 유리가 있습니다.
- 무알칼리 유리 (Alkali-Free Glass): 알칼리 금속 성분 (나트륨, 칼륨 등) 을 최소화하여 만든 유리입니다. 알칼리 이온은 박막 트랜지스터 (TFT) 소자의 성능 저하를 유발할 수 있기 때문에, LCD, OLED 등 평판 디스플레이 기판, AMOLED 봉지재료 (Encapsulation) 등에 주로 사용됩니다. 대표적인 예시로 코닝(Corning)의 이글 XG (Eagle XG), AGC의 렉사글라스 (Lexiglas) 등이 있습니다.
- 석영 유리 (Quartz Glass / Fused Silica): 순수한 이산화규소(SiO₂)로만 이루어진 유리입니다. 매우 높은 순도, 뛰어난 내열성 (1000℃ 이상), 높은 광 투과율 (자외선 영역까지 투과), 낮은 열팽창 계수, 우수한 화학적 안정성 등 최상급의 특성을 자랑합니다. 반도체 공정용 마스크 기판, 고성능 광학 소자, UV 램프, 고온 실험 장비 등에 사용되며, 가격이 매우 비쌉니다.
- 특수 기능성 유리: 특정 기능 (예: 화학 강화, 방사선 차폐, 색상 구현, 저반사, 발광 등) 을 부여하기 위해 특수 성분을 첨가하거나 표면 처리한 유리입니다. 용도에 따라 다양한 종류가 존재하며, 스마트폰 커버 유리 (화학 강화 유리), X-ray 차폐 유리, 칼라 필터 유리, AR 코팅 유리, 형광 유리 등이 있습니다.
- 유리기판의 주요 응용 분야:
- 평판 디스플레이 (FPD): LCD (액정 디스플레이), OLED (유기 발광 다이오드), 마이크로 LED 디스플레이 등 다양한 평판 디스플레이의 핵심 기판 소재입니다. TFT 기판, 칼라 필터 기판, 봉지 기판 등으로 사용됩니다.
- 태양 전지 (Solar Cells): 결정질 실리콘 태양 전지, 박막 태양 전지 (아몰퍼스 실리콘, CIGS, CdTe 등) 의 커버 유리, 기판 유리로 사용됩니다. 태양 전지 모듈을 보호하고, 빛을 투과시키는 역할을 합니다.
- 터치스크린 패널 (Touch Screen Panel, TSP): 스마트폰, 태블릿 PC, 노트북, 키오스크 등 터치스크린 패널의 커버 윈도우, 센서 기판 등으로 사용됩니다. 뛰어난 투명도와 내구성이 요구됩니다.
- 센서 (Sensors): 이미지 센서, 바이오 센서, 압력 센서, 가스 센서 등 다양한 센서 소자의 기판으로 활용됩니다. 특정 파장 영역에서의 투과율, 화학적 안정성, 절연 특성 등이 요구될 수 있습니다.
- 반도체 패키징 (Semiconductor Packaging): 유리 인터포저 (Glass Interposer), 팬아웃 웨이퍼 레벨 패키징 (Fan-Out Wafer Level Packaging, FOWLP) 등 차세대 반도체 패키징 기술에 유리기판이 적용되고 있습니다. 고밀도 배선, 미세 회로 패턴 형성, 우수한 전기적 특성, 얇은 두께 구현 등이 가능합니다.
- 기타 광학 소자 및 부품: 렌즈, 프리즘, 광섬유, 광도파로, 광학 필터, 미러, 빔 스플리터 등 다양한 광학 소자 및 부품 제작에 유리가 사용됩니다.
- 평판 디스플레이 (FPD): LCD (액정 디스플레이), OLED (유기 발광 다이오드), 마이크로 LED 디스플레이 등 다양한 평판 디스플레이의 핵심 기판 소재입니다. TFT 기판, 칼라 필터 기판, 봉지 기판 등으로 사용됩니다.
2. 유리 웨이퍼 (Glass Wafer)
유리 웨이퍼는 유리기판 중에서 특히 반도체 공정에 사용될 수 있도록 정밀하게 가공된 얇은 원판 형태의 유리기판을 지칭하는 용어입니다. 일반적으로 실리콘 웨이퍼와 유사한 형태와 공정으로 제작되며, 실리콘 웨이퍼를 대체하거나 보완하는 용도로 활용될 가능성이 높아 연구 개발이 활발하게 진행되고 있습니다. 여기서 '웨이퍼(wafer)'는 반도체 집적 회로를 제조하는 데 사용되는 얇고 둥근 판 형태의 기판을 의미합니다.
- 유리 웨이퍼의 특징:
- 정밀 가공된 박막 원판: 일반 유리기판에 비해 두께가 훨씬 얇고 (수십 μm ~ 수백 μm), 표면 평탄도, 두께 균일도, 표면 청정도 등 반도체 공정 요구 조건에 맞춰 엄격하게 관리됩니다. 정밀 연마 (Polishing), 세정 (Cleaning), 엣지 그라인딩 (Edge Grinding) 등의 공정을 거쳐 제작됩니다.
- 실리콘 웨이퍼와 유사한 형태: 원형 (주로), 사각형 등 다양한 형태가 가능하지만, 반도체 공정 장비 호환성을 위해 원형 웨이퍼 형태가 일반적입니다. 크기 또한 실리콘 웨이퍼와 유사한 규격 (예: 4인치, 6인치, 8인치, 12인치) 으로 제작됩니다.
- 다양한 유리 조성 활용: 소다라임 유리, 붕규산 유리, 무알칼리 유리, 석영 유리 등 다양한 유리 조성을 유리 웨이퍼 제작에 활용할 수 있습니다. 응용 분야 및 요구 성능에 따라 최적의 유리 조성을 선택합니다.
- 실리콘 웨이퍼 대체 및 보완: 유리 웨이퍼는 실리콘 웨이퍼를 완전히 대체하기보다는, 특정 응용 분야에서 실리콘 웨이퍼의 한계를 극복하거나 보완하는 역할을 목표로 합니다. 예를 들어, 대면적, 초박막, 고주파, 광학적 특성 활용, 저비용 공정 등의 장점을 활용하여 새로운 반도체 소자 및 공정 기술을 구현하는 데 기여할 수 있습니다.
- 유리 웨이퍼의 장점 (실리콘 웨이퍼 대비):
- 저렴한 소재 비용: 유리 원재료는 실리콘에 비해 저렴하고, 웨이퍼 제조 공정도 비교적 간단하여 웨이퍼 가격을 낮출 수 있습니다. 특히 대면적 웨이퍼 제조 시 비용 절감 효과가 더욱 커집니다.
- 우수한 절연 특성 및 저유전율: 유리는 실리콘에 비해 우수한 절연 특성을 가지며, 저유전율 특성을 가진 유리를 선택하면 고주파 소자 성능 향상에 유리합니다. 5G/6G 통신, 고성능 RF 소자, 혼성 집적 회로 (Heterogeneous Integration) 등에 응용 가능성이 높습니다.
- 광학적 특성 활용 용이: 유리의 높은 광 투과율을 활용하여 광학 소자 집적, 실리콘 포토닉스 (Silicon Photonics) 기술, 광 센서, 투명 디스플레이 등 새로운 기능의 반도체 소자 개발에 유리합니다.
- 대면적 웨이퍼 제조 용이: 유리 용융 및 성형 기술을 활용하여 실리콘 웨이퍼 대비 더 큰 면적의 웨이퍼 (예: 300mm 이상) 를 비교적 용이하게 제조할 수 있습니다. 대면적 웨이퍼는 생산성 향상 및 비용 절감에 기여합니다.
- 초박막 웨이퍼 제조 용이: 유리는 얇게 가공하기 용이하여 초박막 웨이퍼 (수십 μm 이하) 제조에 유리합니다. 적층형 반도체 소자, 플렉서블 디스플레이, 웨어러블 기기 등에 응용 가능성이 높습니다.
- 유리 웨이퍼의 단점 (실리콘 웨이퍼 대비):
- 낮은 열전도율: 유리는 실리콘에 비해 열전도율이 매우 낮아 고전력 소자, 고집적 소자의 방열 문제에 취약합니다. 열 관리 기술 (방열 설계, 냉각 기술 등) 과 함께 사용해야 합니다.
- 낮은 결정성 및 캐리어 이동 속도: 유리는 비정질 (amorphous) 또는 다결정 (polycrystalline) 구조를 가지므로, 실리콘 단결정 웨이퍼에 비해 캐리어 이동 속도가 현저히 낮습니다. 고성능 트랜지스터, 고속 논리 회로 등에는 적용이 어렵습니다.
- 가공의 어려움: 유리는 깨지기 쉽고, 정밀 식각, 도핑 등 반도체 공정 기술 적용에 어려움이 있습니다. 실리콘 공정 장비 및 기술을 그대로 활용하기 어렵고, 유리 맞춤형 공정 기술 개발이 필요합니다.
- 신뢰성 및 내구성 문제: 유리는 기계적 강도, 내습성, 내열충격성 등이 실리콘에 비해 떨어질 수 있습니다. 가혹한 환경에서 소자 신뢰성 및 수명 확보에 어려움이 있을 수 있습니다.
- 유리 웨이퍼의 주요 응용 분야:
- 유리 인터포저 (Glass Interposer): 실리콘 인터포저를 대체하여 고성능 반도체 패키징에 사용됩니다. 우수한 전기적 특성 (저유전율, 낮은 신호 손실), 미세 배선 구현 용이성, 저비용 등의 장점을 활용합니다. 고대역폭 메모리 (HBM), 고성능 컴퓨팅 (HPC) 칩, 2.5D/3D 집적 회로 등에 적용될 수 있습니다.
- 팬아웃 웨이퍼 레벨 패키징 (FOWLP) 용 재분배층 (RDL) 기판: FOWLP 기술에서 칩과 외부 회로를 연결하는 재분배층 (RDL) 기판으로 유리 웨이퍼를 활용합니다. 대면적, 박막 유리 웨이퍼의 장점을 활용하여 패키징 면적을 넓히고, 박막화, 경량화를 구현합니다.
- 실리콘 포토닉스 (Silicon Photonics) 용 웨이퍼: 실리콘 웨이퍼 기반 광 집적 회로 (Photonic Integrated Circuit, PIC) 제작 시, 광 도파로 (Optical Waveguide) 층 또는 광학 소자 (Optical Devices) 제작용 기판으로 유리 웨이퍼를 사용합니다. 실리콘의 전기적 특성과 유리의 광학적 특성을 결합하여 고성능 광통신 칩, 광 센서 등을 구현합니다.
- 초박막 트랜지스터 (Thin-Film Transistor, TFT) 기판: 플렉서블 디스플레이, 투명 디스플레이, 웨어러블 기기 등에 적용되는 초박막 트랜지스터 (TFT) 소자의 기판으로 유리 웨이퍼를 사용합니다. 유리의 투명성, 유연성, 저온 공정 가능성 등을 활용합니다.
- 바이오/화학 센서 (Bio/Chemical Sensors): 유리의 화학적 안정성, 생체 적합성, 광학적 특성 등을 활용하여 바이오 센서, 화학 센서, 미세 유체 칩 (Microfluidic Chip) 등 제작에 유리 웨이퍼를 응용합니다.
- 유리 인터포저 (Glass Interposer): 실리콘 인터포저를 대체하여 고성능 반도체 패키징에 사용됩니다. 우수한 전기적 특성 (저유전율, 낮은 신호 손실), 미세 배선 구현 용이성, 저비용 등의 장점을 활용합니다. 고대역폭 메모리 (HBM), 고성능 컴퓨팅 (HPC) 칩, 2.5D/3D 집적 회로 등에 적용될 수 있습니다.
3. 유리 웨이퍼 vs 유리기판 비교 요약
정의 | 넓은 의미의 유리 소재 기판. 다양한 형태와 크기, 유리 조성 포함 | 반도체 공정용으로 정밀 가공된 박막 원판 형태의 유리기판 |
형태 | 판, 시트, 블록, 필름 등 다양한 형태 가능 | 주로 원판 (Wafer) 형태, 실리콘 웨이퍼와 유사한 규격 |
두께 | 비교적 두꺼움 (수백 μm ~ 수 mm 이상) | 얇음 (수십 μm ~ 수백 μm) |
표면 | 평탄하지만, 웨이퍼 수준의 고정밀도는 아님 | 고도의 표면 평탄도, 두께 균일도, 표면 청정도를 가짐 |
가공 정밀도 | 비교적 낮음 | 높음 (반도체 공정 요구 조건 충족) |
주요 용도 | FPD, 태양 전지, 터치스크린, 일반 센서, 커버 유리 등 | 반도체 공정용 기판 (인터포저, FOWLP용 RDL, 실리콘 포토닉스, 초박막 TFT 등) |
가격 | 유리 조성, 크기, 가공 정도에 따라 다양 | 유리기판 대비 고가, 실리콘 웨이퍼 대비 저렴 (잠재적) |
4. 비용 비교
일반적으로 유리기판은 유리 웨이퍼보다 저렴합니다. 유리기판은 대량 생산되는 범용 소재이며, 가공 정밀도 요구 수준이 유리 웨이퍼에 비해 낮기 때문입니다. 유리 웨이퍼는 반도체 공정용으로 정밀하게 가공되어야 하므로, 제조 공정이 더 복잡하고 비용이 많이 듭니다. 하지만, 유리 웨이퍼는 실리콘 웨이퍼에 비해 잠재적으로 저렴한 비용으로 대면적 웨이퍼를 생산할 수 있는 가능성을 가지고 있습니다.
5. 결론
유리기판과 유리 웨이퍼는 모두 유리 소재를 기반으로 하지만, 유리 웨이퍼는 유리기판의 한 종류이며, 특히 반도체 공정에 특화된 고정밀 유리기판이라고 할 수 있습니다. 유리기판은 보다 넓은 범위의 유리 소재 기판을 포괄하는 일반적인 용어이며, 유리 웨이퍼는 반도체 산업이라는 특정 분야에서 사용되는 전문 용어에 가깝습니다.
일상적인 상황에서는 "유리기판"이라는 용어를 포괄적으로 사용해도 무방하지만, 반도체 공정, 반도체 소자, 웨이퍼 레벨 패키징 등 특정 기술 분야를 논할 때는 "유리 웨이퍼"라는 용어를 사용하는 것이 더 정확합니다. 두 용어 모두 상황에 따라 혼용될 수 있지만, 그 의미와 뉘앙스 차이를 이해하고 사용하는 것이 중요합니다.
더 궁금한 점이나 특정 응용 분야에 대한 질문이 있으시면 언제든지 다시 문의해주세요.
HBM (High Bandwidth Memory) 용 유리기판
HBM (High Bandwidth Memory) 은 고성능 컴퓨팅, 인공지능, 그래픽 카드 등 최고 성능을 요구하는 분야에서 핵심적인 역할을 하는 고대역폭 메모리 기술입니다. 최근 HBM의 성능 향상과 함께, 기존 실리콘 인터포저를 대체할 유리기판이 차세대 HBM 패키징 기술의 게임 체인저로 주목받고 있습니다.
HBM 용 유리기판은 단순히 유리를 HBM에 사용하는 것을 넘어, HBM 성능을 극대화하고, 패키징 기술의 혁신을 가져올 수 있는 핵심 기술입니다. 이 글에서는 HBM 용 유리기판에 대한 자세하고 포괄적인 정보를 제공하여 사용자님의 궁금증을 해소하고, HBM과 유리기판 기술에 대한 깊이 있는 이해를 돕고자 합니다.
1. HBM (High Bandwidth Memory) 이란?
HBM은 High Bandwidth Memory의 약자로, 높은 대역폭을 제공하는 고성능 메모리 기술입니다. CPU, GPU, ASIC 등 고성능 프로세서와 함께 사용되어 데이터를 빠르게 처리하고, 대용량 데이터를 효율적으로 전송하는 데 필수적인 역할을 합니다.
- HBM의 특징:
- 높은 대역폭 (High Bandwidth): 기존 DDR5 메모리 대비 수 배에서 수십 배 더 넓은 대역폭을 제공하여 데이터 병목 현상을 해소하고 시스템 성능을 극대화합니다.
- 적층 구조 (Stacked Structure): 여러 개의 DRAM 칩을 수직으로 적층하여 패키지 크기를 줄이면서도 메모리 용량과 대역폭을 획기적으로 증가시킵니다.
- 짧은 데이터 경로 (Short Data Path): 칩을 수직으로 적층하고 TSV (Through Silicon Via, 실리콘 관통 전극) 기술을 사용하여 데이터 이동 거리를 최소화하여 전력 효율을 높입니다.
- 고성능 컴퓨팅 (HPC), AI 가속기, 그래픽 카드 등 최첨단 분야에 필수적인 메모리 솔루션입니다.
- HBM의 발전 단계:
- HBM: 최초의 HBM 표준
- HBM2: HBM 대비 대역폭 및 용량 향상
- HBM2E: HBM2 성능 개선 버전, 현재 가장 널리 사용되는 표준
- HBM3: HBM2E 대비 대역폭 및 용량 대폭 향상, 차세대 고성능 메모리
- HBM3E: HBM3 성능 개선 및 전력 효율 향상 버전, 2025년 이후 주력 제품으로 예상
- HBM4, HBMnext: 미래 HBM 기술, 더욱 높은 대역폭 및 용량 목표
2. HBM 패키징과 인터포저 (Interposer)
HBM은 여러 개의 DRAM 칩을 적층하고, 이를 프로세서와 연결하기 위해 첨단 패키징 기술이 필수적입니다. 여기서 핵심적인 역할을 하는 것이 인터포저 (Interposer) 입니다.
- 인터포저 (Interposer) 란?
- 칩과 칩 사이를 연결하는 중간 기판: CPU, GPU 와 같은 로직 칩과 HBM 메모리 칩을 전기적으로 연결하는 역할을 합니다.
- 고밀도 배선 (High-Density Interconnect): 미세한 배선을 통해 칩 간의 데이터 및 전력 신호를 효율적으로 전달합니다.
- 다층 구조 (Multi-Layer Structure): 복잡한 배선 구조를 구현하기 위해 다층 기판 형태로 제작됩니다.
- 인터포저의 역할:
- 전기적 연결 (Electrical Connection): 로직 칩과 HBM 칩 간의 수많은 입출력 (I/O) 신호를 연결하여 데이터 통로를 제공합니다.
- 신호 무결성 (Signal Integrity) 유지: 고속, 고대역폭 데이터 전송 시 신호 손실 및 왜곡을 최소화하여 시스템 성능을 유지합니다.
- 전력 분배 (Power Delivery): 각 칩에 안정적으로 전력을 공급하는 역할을 합니다.
- 열 방출 (Heat Dissipation) 보조: 칩에서 발생하는 열을 외부로 효과적으로 분산시키는 역할을 일부 수행합니다.
- 기존 인터포저: 실리콘 인터포저 (Silicon Interposer)
- 실리콘 웨이퍼 기반: 반도체 공정 기술을 활용하여 실리콘 웨이퍼 위에 미세 배선을 형성하여 제작합니다.
- 성숙된 기술: 오랜 기간 사용되어 온 기술로, 안정적인 성능과 생산 기술을 확보하고 있습니다.
- 높은 생산 비용: 실리콘 웨이퍼 자체가 고가이며, 복잡한 미세 공정 기술이 필요하여 생산 비용이 높습니다.
- 기술적 한계: 미세 배선 밀도 증가, 대면적 인터포저 제작, 전기적 특성 향상 등에서 기술적인 한계에 직면하고 있습니다. 특히, 실리콘의 높은 유전율은 신호 손실 및 전력 소모 증가의 원인이 됩니다.
3. HBM 용 유리기판 (Glass Substrate for HBM) 의 등장
실리콘 인터포저의 한계를 극복하고 HBM 성능을 더욱 향상시키기 위한 대안으로 유리기판이 주목받기 시작했습니다. 유리기판은 실리콘 대비 저렴한 비용, 우수한 전기적 특성, 미세 패턴 형성 용이성 등 다양한 장점을 제공하여 차세대 HBM 인터포저 소재로 각광받고 있습니다.
- 유리기판 인터포저의 장점:
- 저비용 (Low Cost):
- 유리 원재료 가격 저렴: 실리콘 웨이퍼 대비 유리 원재료 가격이 훨씬 저렴합니다.
- 간단한 제조 공정: 실리콘 인터포저 대비 공정이 단순하여 생산 비용을 절감할 수 있습니다.
- 대면적 웨이퍼 생산 용이: 유리 기판은 대면적으로 제작하기 용이하여 대량 생산 시 규모의 경제를 확보할 수 있습니다.
- HBM 가격 경쟁력 향상: 유리기판 인터포저를 통해 HBM 생산 비용을 절감하여 HBM 가격 경쟁력을 높일 수 있습니다.
- 우수한 전기적 특성 (Excellent Electrical Performance):
- 낮은 유전율 (Low Dielectric Constant): 유리는 실리콘 대비 유전율이 현저히 낮습니다. (유리: 4~7, 실리콘: 11.9)
- 신호 손실 감소: 낮은 유전율은 전기 신호의 손실을 줄여 신호 무결성을 향상시키고, 데이터 전송 속도를 높여줍니다. 특히 고주파, 고대역폭 환경에서 유리한 특성입니다.
- 전력 소모 감소: 낮은 유전율은 기생 용량 (Parasitic Capacitance) 을 감소시켜 전력 소모를 줄여줍니다. HBM과 같은 고성능 메모리에서 전력 효율은 매우 중요한 요소입니다.
- HBM 성능 향상: 유리기판 인터포저를 통해 HBM의 대역폭, 속도, 전력 효율을 획기적으로 향상시킬 수 있습니다.
- 미세 패턴 형성 용이 (Fine Patterning Capability):
- 매끄러운 표면: 유리 기판은 매우 매끄러운 표면을 가지고 있어 미세 패턴 형성에 유리합니다.
- 고밀도 배선 구현: 미세 패턴 형성 기술을 통해 인터포저 내 배선 밀도를 높여 칩 간 연결 효율을 극대화할 수 있습니다.
- HBM 집적도 향상: 고밀도 배선 기술은 HBM의 집적도를 높여 더 작은 면적에 더 많은 메모리 용량을 구현할 수 있도록 합니다.
- 초미세 회로 구현 가능성: 유리 기판은 차세대 반도체 공정 기술인 서브 마이크로미터 (Sub-Micrometer) 회로 구현에도 적합하여 미래 반도체 기술 발전에 기여할 수 있습니다.
- 대면적 기판 (Large Area Substrate) 용이:
- 대형 패널 생산 기술: 유리 기판은 디스플레이 산업에서 대형 패널 생산 기술이 발달되어 있어 대면적 웨이퍼 형태로 제작하기 용이합니다.
- 수율 향상 및 비용 절감: 대면적 웨이퍼를 통해 생산성을 높이고, 웨이퍼당 칩 생산량을 늘려 비용 절감 효과를 얻을 수 있습니다.
- 다양한 칩 통합 용이: 대면적 유리기판 인터포저는 더 많은 수의 칩 (CPU, GPU, HBM, I/O 칩 등) 을 하나의 패키지에 통합하는 것을 가능하게 하여 시스템 통합 수준을 높일 수 있습니다.
- 칩렛 (Chiplet) 통합에 유리: 다양한 기능을 가진 칩렛들을 유리기판 인터포저 위에 통합하여 맞춤형 고성능 시스템을 유연하게 설계할 수 있습니다.
- 저비용 (Low Cost):
- 유리기판 인터포저 기술 개발의 주요 목표:
- 실리콘 인터포저 대체: 고성능 HBM 시장에서 실리콘 인터포저를 대체하여 비용 효율적이고 성능이 향상된 인터포저 솔루션 제공
- HBM 성능 극대화: 유리기판의 장점을 활용하여 HBM의 대역폭, 속도, 전력 효율을 획기적으로 향상
- 패키징 기술 혁신: 유리기판 기반의 새로운 패키징 기술을 개발하여 반도체 산업의 미래 성장 동력 확보
- 차세대 반도체 기술 선도: 유리기판 인터포저 기술을 통해 서브 마이크로미터 회로 및 3D 집적 회로 시대를 앞당기고, 반도체 기술 혁신 주도
4. HBM 용 유리기판 기술 개발의 도전 과제
유리기판 인터포저는 HBM 패키징 기술의 혁신을 가져올 잠재력을 가지고 있지만, 상용화를 위해서는 극복해야 할 기술적인 과제들이 남아있습니다.
- 낮은 열전도율 (Low Thermal Conductivity):
- 유리의 낮은 열전도율: 유리는 실리콘 대비 열전도율이 낮아 (유리: ~1 W/mK, 실리콘: 150 W/mK) 칩에서 발생하는 열을 효과적으로 방출하기 어렵습니다.
- HBM 발열 문제 심화: HBM은 고성능 동작 시 발열량이 많으므로, 유리기판 인터포저 사용 시 열 관리 문제가 더욱 중요해집니다.
- 열 설계 및 냉각 기술 필요: 유리기판 인터포저의 열 방출 특성을 개선하기 위한 새로운 열 설계 기술 (방열 패턴 설계, 열 인터페이스 물질 적용 등) 및 효과적인 냉각 기술 (액체 냉각, 히트 파이프 등) 개발이 필수적입니다.
- 낮은 기계적 강도 및 취성 (Low Mechanical Strength & Brittleness):
- 유리의 취약한 기계적 특성: 유리는 실리콘 대비 기계적 강도가 약하고 깨지기 쉽습니다. 특히 얇은 유리기판은 외부 충격이나 힘에 의해 파손될 위험이 높습니다.
- 핸들링 및 공정 어려움: 얇은 유리기판을 웨이퍼 레벨 공정에서 안전하게 다루고, 칩을 적층하는 과정에서 파손 없이 핸들링하는 기술이 중요합니다.
- 기판 강화 기술 필요: 유리 기판의 기계적 강도를 높이기 위한 화학 강화 유리, 필름 코팅, 지지체 결합 등 다양한 강화 기술 개발이 필요합니다.
- 신뢰성 확보: 유리기판 인터포저 기반 HBM 패키지의 기계적 신뢰성 (충격, 진동, 굽힘 등) 을 확보하는 것이 중요합니다.
- 관통 전극 (TSV) 형성 기술 (Through Glass Via, TGV):
- 유리 TSV 형성의 어려움: 실리콘 TSV 대비 유리 TSV 형성 공정은 기술적인 난이도가 높습니다. 유리는 절연체이며, 식각 속도 제어, 도전체 금속 채우기 등에서 어려움이 있습니다.
- 고성능 TGV 기술 개발: 유리기판 인터포저 기반 HBM의 성능을 극대화하기 위해서는 고밀도, 고종횡비, 저저항 TGV 형성 기술 개발이 필수적입니다.
- 레이저 드릴링, 습식/건식 식각, 플라즈마 식각, 메탈 필링 등 다양한 유리 TSV 형성 기술이 연구되고 있습니다. 각 기술의 장단점을 분석하고, HBM 요구 조건에 최적화된 기술을 개발해야 합니다.
- 정밀도 높은 본딩 (Bonding) 기술:
- 유리-칩 본딩 정밀도: 유리기판 인터포저 위에 HBM 칩, 로직 칩 등을 정밀하게 본딩하는 기술이 중요합니다. 특히 고밀도 배선을 통해 칩 간 연결을 구현해야 하므로, 높은 정렬 정확도와 본딩 강도가 요구됩니다.
- 열팽창 계수 차이 (CTE Mismatch): 유리, 실리콘, DRAM 칩 등 이종 재료 간 열팽창 계수 차이로 인해 본딩 계면에 잔류 응력이 발생할 수 있습니다. 본딩 신뢰성 저하 및 소자 성능에 영향을 미칠 수 있으므로, 열팽창 계수 차이를 완화하는 본딩 기술 개발이 필요합니다.
- 하이브리드 본딩, 하이브리드 금속 본딩, TCB (Thermocompression Bonding) 등 다양한 본딩 기술이 유리기판 인터포저에 적용될 수 있으며, 각 기술의 장단점을 고려하여 최적의 본딩 솔루션을 선택해야 합니다.
- 신뢰성 및 수명 (Reliability & Lifetime) 검증:
- 가혹한 환경 조건: HBM은 고성능 컴퓨팅 환경에서 고속으로 동작하므로, 높은 온도, 습도, 전압 스트레스 등 가혹한 환경 조건에서 장시간 안정적으로 동작해야 합니다.
- 장기 신뢰성 테스트: 유리기판 인터포저 기반 HBM 패키지의 장기 신뢰성 (온도 사이클 테스트, 고온 고습 테스트, 수명 예측 등) 을 철저하게 검증해야 합니다.
- 품질 관리 시스템 구축: 유리기판 인터포저의 균일한 품질을 확보하고, 불량률을 최소화하기 위한 체계적인 품질 관리 시스템 구축이 필수적입니다.
- 자동차, 데이터센터, 의료 등 높은 신뢰성을 요구하는 응용 분야에 적용하기 위해서는 더욱 엄격한 품질 기준과 신뢰성 검증 절차가 필요합니다.
5. HBM 용 유리기판 최신 기술 동향 (2025년 기준)
2025년 현재, HBM 용 유리기판 기술은 연구 개발 단계를 넘어 상용화 초기 단계에 진입하고 있습니다. 글로벌 반도체 기업, 소재 기업, 장비 기업들이 HBM 용 유리기판 기술 개발에 적극적으로 투자하고 있으며, 구체적인 성과들이 가시화되고 있습니다.
- 주요 기업들의 HBM 용 유리기판 개발 경쟁:
- 인텔 (Intel): 유리기판 인터포저 기술 개발에 가장 적극적인 기업 중 하나입니다. 2023년부터 유리기판 인터포저 기반의 차세대 패키징 기술을 공개하며 기술 리더십을 강조하고 있습니다. 2025년 이후 HBM 및 고성능 컴퓨팅 칩에 유리기판 인터포저를 적용할 계획을 발표했습니다.
- 삼성전자 (Samsung Electronics) & SK하이닉스 (SK Hynix): HBM 시장 점유율 1, 2위 기업으로서 유리기판 기술 개발에 높은 관심을 보이고 있습니다. 유리기판 인터포저의 기술 동향을 주시하며, 장기적인 관점에서 HBM 적용 가능성을 검토하고 있는 것으로 알려져 있습니다. 유리기판 소재 기업과의 협력을 통해 기술 개발에 참여할 가능성도 높습니다.
- TSMC (Taiwan Semiconductor Manufacturing Company): 파운드리 1위 기업으로서 InFO_G (Integrated Fan-Out Glass) 기술을 개발하고 있습니다. InFO_G 기술은 유리기판을 활용한 팬아웃 웨이퍼 레벨 패키징 기술로, HBM 및 고성능 칩 패키징에 적용될 수 있습니다. 고객사 (AMD, 엔비디아 등) 와 협력하여 InFO_G 기술의 상용화를 추진하고 있습니다.
- AMD & 엔비디아 (NVIDIA): 고성능 CPU, GPU 설계 기업으로서 HBM 성능 향상에 매우 큰 관심을 가지고 있습니다. 유리기판 인터포저 기술의 개발 동향을 주시하며, 자사의 차세대 칩에 유리기판 인터포저를 적용하는 방안을 적극적으로 검토할 것으로 예상됩니다. TSMC InFO_G 기술의 주요 고객이 될 가능성이 높습니다.
- 소재 및 장비 기업들의 기술 혁신:
- Corning & AGC: 유리기판 소재 분야의 선두 기업으로서 HBM 용 유리기판 개발에 주력하고 있습니다. 고강도, 고내열성, 저유전율 특성을 가진 특수 유리 조성 개발, 대면적, 초박막 유리기판 제조 기술 혁신, 유리 웨이퍼 가공 기술 개발 등에 집중하고 있습니다. 반도체 기업들과 협력하여 유리기판 인터포저 상용화를 추진하고 있습니다.
- Applied Materials & LAM Research: 반도체 장비 분야의 선두 기업으로서 유리기판 공정 장비 개발에 박차를 가하고 있습니다. 유리 웨이퍼 핸들링 장비, 정밀 연마 장비, 식각 장비, 박막 증착 장비, 본딩 장비 등 유리기판 인터포저 제조에 필요한 핵심 장비 개발에 주력하고 있습니다. 유리기판 인터포저 생산 라인 구축을 위한 턴키 솔루션 제공을 목표로 하고 있습니다.
- 학계 및 연구 기관의 연구 활발:
- 유리기판 인터포저 기술의 학문적 탐구: 대학교 및 연구 기관에서 유리기판 인터포저의 재료 특성 분석, 설계 최적화, 공정 기술 개발, 신뢰성 평가 등 다양한 연구가 활발하게 진행되고 있습니다.
- 정부 지원 확대: 각국 정부는 미래 반도체 기술 경쟁력 확보를 위해 유리기판 인터포저 기술 개발에 대한 지원을 확대하고 있습니다. 국책 과제, 산학 협력 프로젝트 등을 통해 유리기판 기술 발전을 가속화하고 있습니다.
- 국제 협력 강화: 유리기판 인터포저 기술은 글로벌 협력이 중요한 분야입니다. 국제 학술 교류, 기술 컨퍼런스, 공동 연구 등을 통해 기술 개발 노하우를 공유하고, 표준화를 추진하는 노력이 필요합니다.
6. HBM 용 유리기판의 미래 전망 및 기대 효과
HBM 용 유리기판 기술은 아직 초기 단계이지만, 성공적으로 상용화될 경우 반도체 산업에 혁명적인 변화를 가져올 것으로 기대됩니다.
- HBM 시장 성장 가속화: 유리기판 인터포저를 통해 HBM 가격 경쟁력을 높이고, 성능을 향상시키면 HBM 시장이 더욱 빠르게 성장할 것으로 예상됩니다. AI, 데이터센터, 고성능 컴퓨팅 시장의 확대와 함께 HBM 수요는 폭발적으로 증가할 것입니다.
- 차세대 반도체 패키징 기술 주도: 유리기판 인터포저는 2.5D/3D 패키징 기술의 새로운 패러다임을 제시하고, 차세대 반도체 패키징 기술 혁신을 주도할 것입니다. 팬아웃 웨이퍼 레벨 패키징 (FOWLP), 칩렛 (Chiplet) 통합, 혼성 집적 (Heterogeneous Integration) 등 다양한 첨단 패키징 기술에 유리기판이 핵심적인 역할을 할 것입니다.
- 반도체 산업 경쟁력 강화: 유리기판 인터포저 기술을 선점하는 기업은 차세대 반도체 시장에서 압도적인 경쟁 우위를 확보할 수 있을 것입니다. 국가적인 차원에서도 유리기판 기술 개발에 대한 투자를 확대하여 반도체 산업 경쟁력을 강화해야 합니다.
- IT 산업 전반에 걸친 파급 효과: HBM 성능 향상은 AI, 클라우드 컴퓨팅, 자율주행, 메타버스 등 미래 IT 기술 발전을 가속화하고, 새로운 서비스와 시장 창출에 기여할 것입니다. 유리기판 기술은 반도체 산업뿐 아니라 IT 산업 전반에 걸쳐 광범위한 파급 효과를 가져올 것입니다.
7. 결론 및 추가 질문
HBM 용 유리기판 기술은 차세대 메모리 기술과 패키징 기술의 융합을 통해 반도체 산업의 미래를 바꿀 혁신적인 기술입니다. 저비용, 고성능, 고집적 특성을 가진 유리기판 인터포저는 HBM 성능을 극대화하고, 반도체 패키징 기술의 새로운 지평을 열 것으로 기대됩니다.
하지만, 유리기판 인터포저의 상용화를 위해서는 낮은 열전도율, 기계적 강도, 가공 기술, 신뢰성 등 극복해야 할 기술적인 과제들이 여전히 남아있습니다. 지속적인 연구 개발과 기술 혁신을 통해 이러한 과제들을 해결하고, HBM 용 유리기판 기술을 성공적으로 상용화하는 것이 반도체 산업의 미래를 좌우할 중요한 과제가 될 것입니다.
HBM 용 유리기판에 대해 더 궁금한 점이 있으시거나, 특정 기술 분야에 대한 자세한 정보가 필요하시면 언제든지 다시 질문해주세요. 제가 아는 범위 내에서 최대한 자세하고 정확하게 답변드리겠습니다.
https://www.etnews.com/20250206000317
삼성전자, 반도체 유리기판 직접 뛰어든다
삼성전자가 반도체 유리기판 시장에 진출한다. 유리기판은 인공지능(AI) 칩과 같은 고성능 반도체 구현을 가능케 하는 핵심 부품이다. 지금까지 상용화된 적 없는 차세대 기판으로, 파운드리·시
www.etnews.com
https://newtechnology.tistory.com/
신기술 신제품 인증 컨설팅
신기술.신제품과 녹색기술제품 인증 컨설팅합니다. (건설.교통.환경.방재.보건.전력등 전문신기술 인증도 포함)
newtechnology.tistory.com
'AI.4차 산업과 5G 기술 trend' 카테고리의 다른 글
반도체 패키징 유리기판 (인터포저)*****심층 분석 (1) | 2025.03.26 |
---|---|
이온풍 드론.비행체와 이온추진 엔진*****구조와 원리 (0) | 2025.03.04 |
유리기판 인터포저의 제조 공정 분석 ***** (HBM 용) (0) | 2025.02.28 |
겨울.여름 ±10도 차이를 보상할 수 있는 미래 기술***** (0) | 2025.02.27 |
GPT-5 예상예측. GPT-5에 최적의 비즈니스 모델***** (2) | 2025.02.22 |